Why Contingency Planning Is Essential for Construction Projects
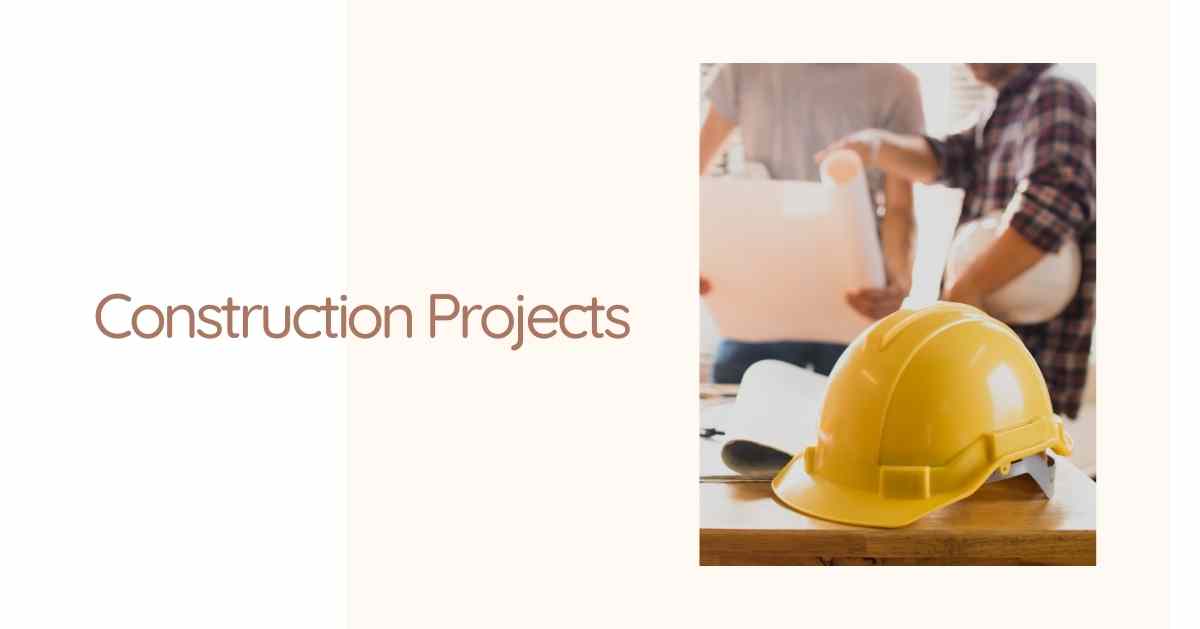
Unexpected issues are a reality in construction. Whether it’s bad weather, supply chain disruptions, or unexpected site conditions, setbacks can cause delays, increase costs, and put project success at risk. This is where contingency planning comes in. Having a well-thought-out strategy for handling unforeseen challenges ensures that projects stay on track and budgets remain under control.
How a Contingency Plan Supports Project Success
A contingency plan isn’t just about preparing for worst-case scenarios—it’s about maintaining flexibility and control when things don’t go as expected. By identifying potential risks in advance and setting aside resources to manage them, builders can minimise disruptions and make informed decisions under pressure.
Many construction teams rely on a construction management platform to track project timelines, budgets, and resource allocation. These tools help builders monitor risks in real-time and adjust plans as needed, ensuring that contingency measures are implemented quickly and effectively.
Common Risks in Construction Projects
Every construction project comes with its own set of risks, but some challenges are more common than others. A strong contingency plan should account for:
1. Weather-Related Delays
Extreme weather conditions—such as heavy rain, high winds, or snow—can halt progress on site. While some delays are unavoidable, having a backup plan can help reduce downtime.
Strategies include:
- Scheduling critical tasks during seasons with more stable weather
- Using temporary covers or heating systems to allow work to continue
- Factoring weather-related delays into the project timeline from the start
2. Material Shortages and Price Fluctuations
Global supply chain disruptions have made it harder to predict material availability and pricing. Builders can prepare for this by:
- Identifying alternative suppliers in case of shortages
- Ordering critical materials in advance when possible
- Setting aside a portion of the budget for unexpected price increases
[Read About: Building the Perfect Tech Setup for Entrepreneurs on a Budget ]
3. Labour Shortages and Scheduling Conflicts
Finding skilled workers has become increasingly difficult in the construction industry. A contingency plan should include:
- Maintaining a network of backup subcontractors
- Cross-training employees to handle multiple roles
- Using scheduling software to avoid overbooking or underutilising workers
4. Unexpected Site Conditions
Soil instability, underground utilities, or hazardous materials can be discovered once excavation begins, leading to costly delays. Conducting thorough site assessments before work starts can help, but a contingency budget should always be in place to handle unexpected site challenges.
5. Regulatory and Permit Issues
Changes in building codes, zoning laws, or unexpected permit delays can disrupt a project. Builders should:
- Stay updated on local regulations
- Work closely with permitting authorities to anticipate potential hold-ups
- Ensure that all required paperwork is submitted early in the process
How to Create a Strong Contingency Plan
A contingency plan should be structured, realistic, and tailored to the specific risks of each project. Here’s how to develop one:
1. Identify Potential Risks
The first step is assessing what could go wrong. This includes evaluating past projects for common setbacks and consulting with stakeholders to anticipate challenges specific to the current build.
2. Allocate a Contingency Budget
Setting aside a contingency fund is crucial for handling unexpected expenses. A typical contingency budget ranges from 5% to 10% of the total project cost, depending on the complexity of the build.
3. Establish Response Strategies
For each identified risk, outline a clear action plan. Who is responsible for making decisions? What steps should be taken if delays or cost overruns occur? Having defined responses helps teams act quickly and efficiently.
4. Communicate the Plan to All Stakeholders
A contingency plan is only effective if everyone involved in the project understands it. Contractors, suppliers, and clients should be aware of potential risks and the steps in place to manage them.
5. Monitor and Adjust as Needed
Risk management doesn’t stop once construction begins. Regular project reviews help teams identify emerging risks early, giving them the opportunity to adjust plans before small issues become major problems.
The Role of Technology in Contingency Planning
Modern construction projects are complex, and keeping track of multiple risks requires efficient tools. A construction management platform helps teams monitor budgets, track scheduling changes, and document risk assessments in real time. By centralising project data, builders can make faster, more informed decisions when unexpected challenges arise.
Conclusion
No construction project goes exactly as planned, but those with strong contingency strategies are far more likely to stay on schedule and within budget. By preparing for common risks, setting aside financial buffers, and using technology to monitor progress, builders can handle unexpected challenges with confidence. A well-executed contingency plan isn’t just a safety net—it’s a proactive approach that keeps projects running smoothly from start to finish.